Home
> Orissa |
 |
|
|
|
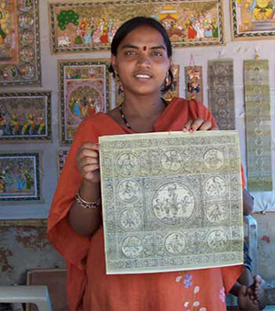 |
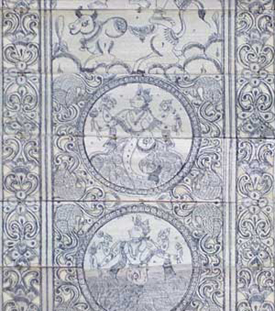 |
|
Orissa
Orissa was famous even in ancient times as an exporter of
textiles to many parts of the civilized world and the handloom craft in Orissa
has survived the ravages of time and still being produced .While buying Orissa
Handlooms you not only cater to the livelyhood of the weavers of Orissa , you
also buy a piece of design which is very ancient. These sarees and other
associated products are produced in the western parts of Orissa in the
districts of Sambalpur and Sonepur and hence more popularly known as the
sambalpuri and sonepuri designs of handloom fabrics.
Though not as super exclusive as the sambalpuri and sonepuri
handlooms , the traditional weavings of Maniabandhs in the district of Cuttack
in the eastern region of orissa is known as Maniabandhi Handlooms and have
survived from the ancient times.Here you will be able to find the traditional
animal motiffs and other desings very typical of Maniabandhi styles.
Maniabandhi products can be termed as value for money product and relatively
cheaper and caters mostly to the needs of the people of Orissa.
WOVEN ON LOOMS
Orissa handlooms have a rich tradition. It's "Tie & Dye" patterns are world
famous. In international parlance, it is well known as IKAT fabrics. The Ikat
technique is commonly known as BANDHA in Orissa. The weavers of Orissa are
class by themselves. They have been known far and wide for the intricate and
painstaking skill exhibited in their fabrics.
A Trip to the textile belt of Orissa is something to be discovered with its
magnificent countryside friendly people and traditional welcome
Nuapatna. This village with many co-operatives of weavers, where centuries of
tradition woven into fabric. The weavers of this village are a class by
themselves. Their TIE & DYE patterns popularly known as 'IKAT' you can
watch all the steps of Ikat Bandha. As per the tradition they weave in silk.
Tasser, ERI silk and also you will be able to follow its way from Cocoons until
the finished fabric.
Sagarpalli to visit Koseleswar weaving factory (Silk &
cotton). Here you will get the idea of design developments, weaving, processing
and mode of training you will also visit some houses, where they make JALLA
work. Proceed to Sonepur you will visit master craftsman. Specially to watch
the best natural lying process ingredients, traditional designs with script in
fabrics. Also visit the pocket loom etc.
|
|
|
|
Bomokai saris of orissa
Legend has two possible theories about the origin of the bomokoi sari. The early rulers had apparently founded many villages, Bomokoi being one among these - the diwan of Bomokoi was a descendant of merchants (from Mantrindi) who had acquired wealth through trade with south-east Asia, and became influential men in Orissa where they settled. They were given estates by Orissa rulers, Bomokoi being one of them. Bomokoi had a few weavers at this time: there is debate about whether the tradition of the bomokoi sari existed in the village (and in Chikita Raj) before the settlers from Mantrindi came, or whether these settlers brought the tradition with them.
Created with the three shuttle weaving technique
and the extra heald shaft design on primitive pit looms, made it a labour
intensive product, and hence expensive. The bomokoi sari was traditionally worn
dominantly by high-caste brahmins during rituals and ceremonies. Certain saris
have specific religious purposes: 'The white badasaara sari is used by the
Soura and Kandha tribes to wrap the statues of their deities whereas the kala
badasaara is draped behind the image of the goddess Thakurani'.
-
Field: The bomokoi are created in coarse low-count count cotton but are always
brightly dyed (often black, red, or white grounds). The body of the sari is
'accented with a single buttah or motif of a bird on a tree.'
-
Borders:
Supplementary weft and warp borders. For the border, popular motifs are
'dalimba or pomegranate corns and saara or seeds topped with a row of kumbha or
temple spires'. Both the 'dalimba and the saara are diamond shaped beads where
the former has a dot within and the saara is halved vertically.'
-
Endpiece: Supplementary weft and warp end-pieces. A broad band
of supplementary warp patterning, creating a latticework of small diamond
shapes is the usual design. The fields warp threads were 'cut and re-tied to
different coloured warps for the endpiece', thus creating an unusually dense
layer of colour for the (fairly large) endpiece. This was known as muha-johra
or 'end-piece with joined threads' (muha = face; johra = join). 'To achieve a
solid colour effect in the pallav, two different coloured warp threads are
twisted with starch and joined at the junction where the pallav and body meet.'
(A muha-johra bada-saara is a sari that is 'blood red in colour and has dotted
diamonds [saara] in the border'.)
In the bomokoi sari, on a 'bright background, the weavers create panels of
contrasting motifs in the anchal or pallav'. The motifs are many: karela or
bitter gourd, the atasi flower, the kanthi phul or small flower, macchi or fly,
rui macchi or carp-fish, koincha or tortoise, padma or lotus, mayura or
peacock, and charai or bird being some of the more common ones. Motifs are
freely composed; unlike other traditional saris, 'the pallav pattern does not
have any regular grading of motifs, like for example, heavy to light'. As
only rich Brahmins wore this sari, each piece was different, thus making each
creation an exclusive one.
Traditionally, vegetable dyes were used: myrobalan for black,
turmeric for yellow, lac for dark red/maroon, girmati or ochre treated with
ghee for light red, and acacia skin for chrome orange. However, in the past few
decades, the weavers (of which there are only seven who weave the bomokoi) buy
dyed yarn.
Source : http://www.craftrevival.org/
This article has been reproduced with the permission of Craft Revival Trust.
|
|
|
|
|
|